辽宁科技大学在模铸方面的工作
辽宁科技大学冶金工程技术中心是原冶金部批准的面向全国的科研单位,自1978年以来,主要从事模铸技术的研究,曾荣获冶金部先进科研集体称号。
自1978-2012年,先后与鞍钢、宝钢、本钢、包钢、上钢五厂、大冶、西宁、大连、抚顺等20个冶金厂矿合作,开发各种模铸钢锭58种。钢种包括模具钢、低合金高强钢、沸腾钢、滚珠钢、合金工具钢、不锈钢、合金结构钢等,锭重从700kg-80t
1. 细长钢锭设计综述
细长钢锭主要应用于锻造或电极坯,由于其高径比较大(一般为3-10),考虑其应用领域不同,采用不同锭模设计方案及浇注工艺。采用中频感应加热冒口,通过优化锭型设计和浇铸工艺,在保证内部质量的前提下,提高成材率。
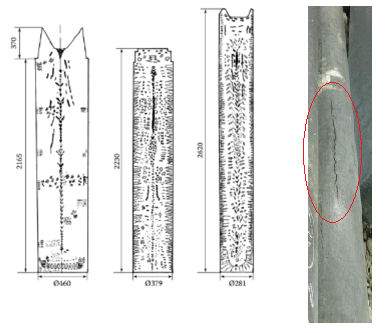
对于电极坯用锭模由于其高径比可达10,且断面为圆形、锥度小(0.35%),冷却效果较波纹形小1.1倍,比同面积方形小1.3倍,冷却效果差,易产生纵向裂纹。
电极坯的设计时主要考虑以下方面:
1. 采用较大的模锭比,减少锭模变形,使脱模容易;
2. 优化浇铸速度、温度,减少偏析和缩孔
3.优化锭型结构,减少其对凝固进程的影响 。
2. 模拟研究概述
本次模拟研究以Φ500电极坯为基准,系统地研究了反射水口砖对注流的影响;浇铸温度、浇铸速度、保温材料的性能、锭模尺寸对凝固过程的影响。
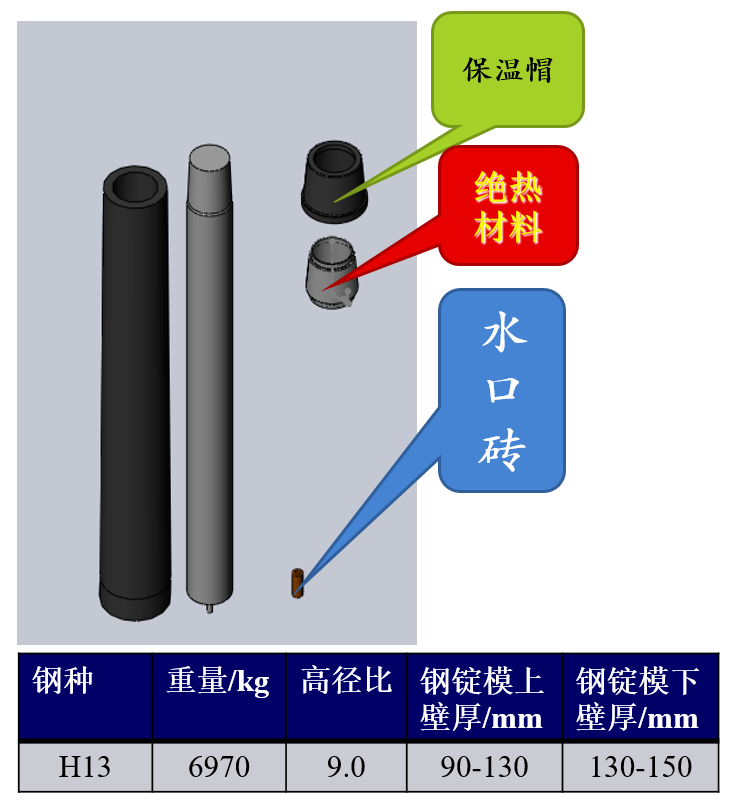
3.1 模拟内容
1. 考虑充型过程速度可调,即开浇快铸,中间慢铸,逐渐加快,帽部慢铸的铸速条件;
2. 考虑充型过程中的温降,按平均每分钟温降0.8℃;
3. 温度场分析,包括锭模、底盘等;
4. 流场分析;
5. 凝固缺陷分析:根据Niyama判据及残余熔体模数、热撕裂判据对缩孔、疏松、等缺陷预测,并对碳偏析进行预测。
3. 2 模拟过程的基本假设
1. 计算涉及材质均为各向同性;
2. 凝固是在平衡条件下进行的;
3. 忽略铸锭及锭模在凝固过程中的变形;
4. 铸件与铸型间的气隙热阻、钢锭与空气的对流换热和辐射换热采用等效换热系数来处理;
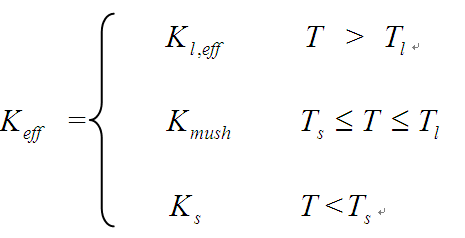
5. 冒口感应加热采用等效的方法,即冒口材料的导热系数设定较低,另外采用冒口加发热剂的方法来等效感应加热冒口效应。
3.3 模拟过程中的材料物性
铸钢材料选则H13作为基本参考材料,其物性参数由AnyCasting自带数据库确定:
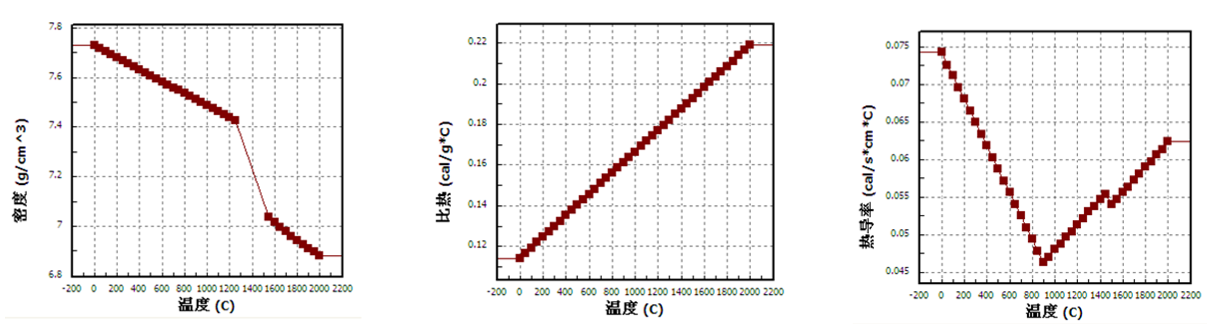
模体和小底盘材料选用灰铁,其物性参数为
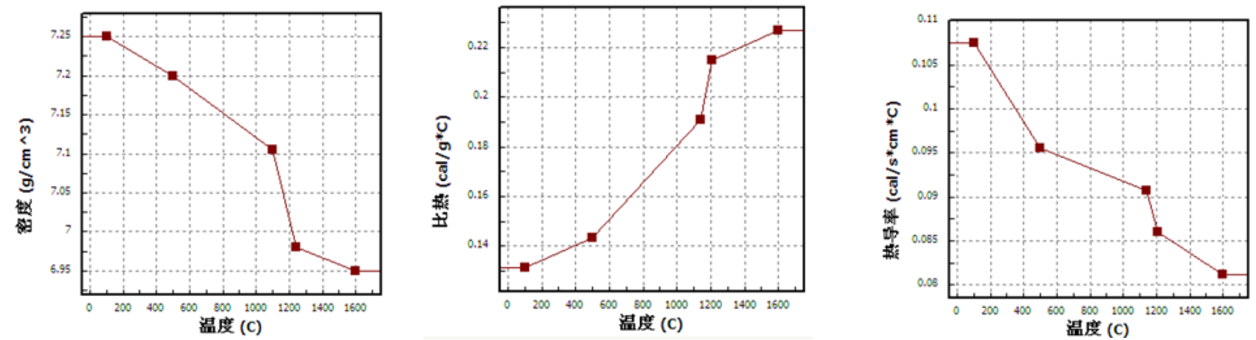
冒口材料选用Al2O3,为了等效中频感应加热效应,其导热系数改为较低的值0.000597086,见表2.2中红色字体(原值为0.0597086)。常规冒口及其它耐火材料的物性参数选用原值。
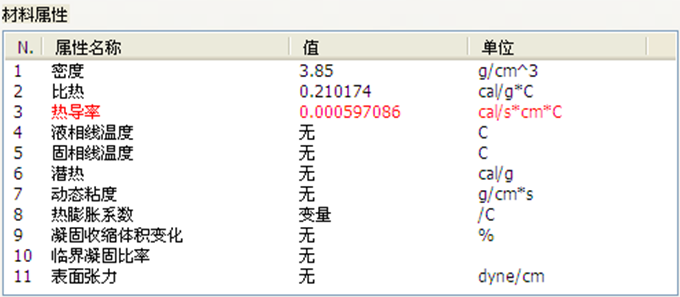
3.4 模拟过程边界条件和初始条件
实际钢锭浇注过程中,钢水充满锭模需要一定时间,这一阶段除了存在强烈的钢水对流外,其冷却传热情况也十分复杂。钢水初始温度为浇注温度,浇铸温度根据浇铸时间降低,大约每分钟下降0.8℃/min.;钢锭模、小底盘的初始温度为80℃,其余材料的初始温度为室温25℃。
3.5 模拟过程换热条件
不同工艺不同的换热系数经验值如下:
空气与任何实体:0.001 cal/(cm2*s*℃)
保温砖与任何实体:0.01 cal/(cm2*s*℃)
模具与模具:0.6 cal/(cm2*s*℃)
模具与铸件(按照温度设置变量):根据液体金属的有效导热系数为固体的2倍左右,即Kl,eff ≈ 2Ks,锭模和铸锭间的有效导热系数如下:
开浇时刻(1511℃):0.01 cal/(cm2*s*℃)
液相线(1471℃):0.004 cal/(cm2*s*℃)
固相线(1404℃):0.003 cal/(cm2*s*℃)
3.6 模拟过程浇口条件
1. 开浇时(填充率为0-3%)为了使钢水能够冲入到锭中,防止钢水在保温砖中凝固阻塞,此时的浇铸速度要高一些;
2. 在液面上升到一定高度以前(填充率为3-30%),熔池液面的波动非常剧烈,容易造成卷渣,因此开浇后要浇速要放慢一些;
3. 当液面上升到一定程度后,浇口与液面落差变小,另外钢水静压力也会阻止注流波动,此时可以加快浇铸速度(填充率为30-90%);
4. 浇到帽部时,根据生产经验此时可再降低浇铸速度,用以补缩,减少缩孔深度。
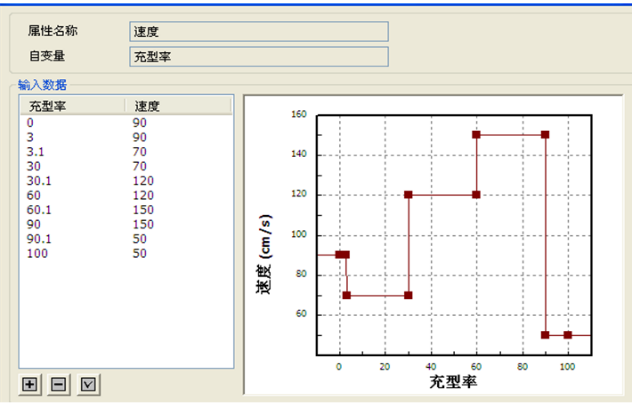
4.基于AnyCasting软件对铸造全过程模拟及缺陷预测
4.1整流水口砖对注流的影响
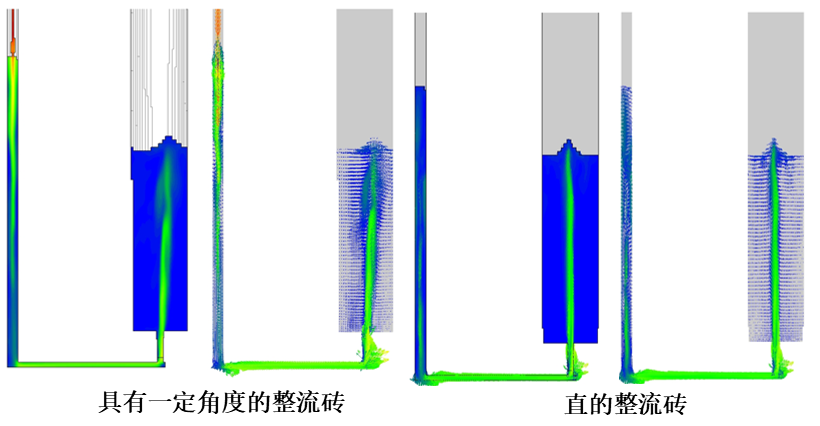
4.2 方案1
Ф500电极坯,浇铸温度1531℃,浇铸速度60cm/s,浇满时间492s,冒口为常规冒口,浇铸后不加发热保护渣,全凝时间5262s,约88分钟
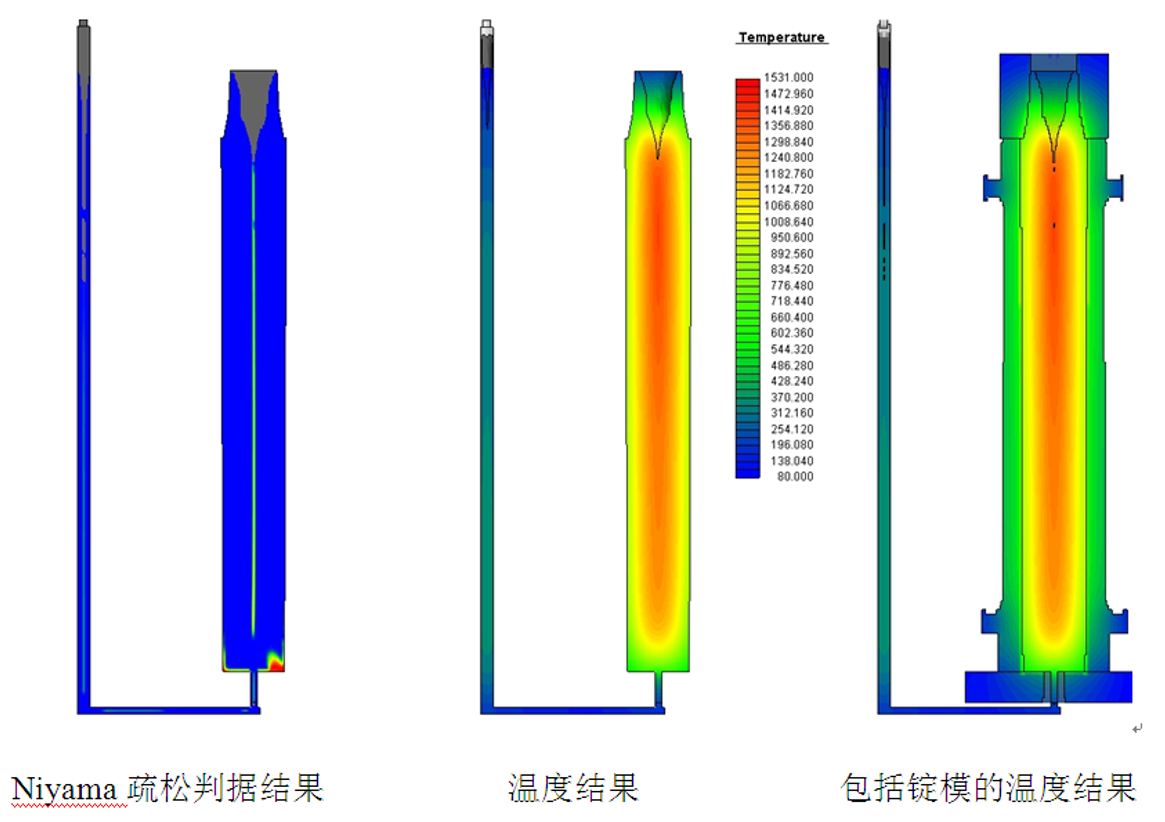
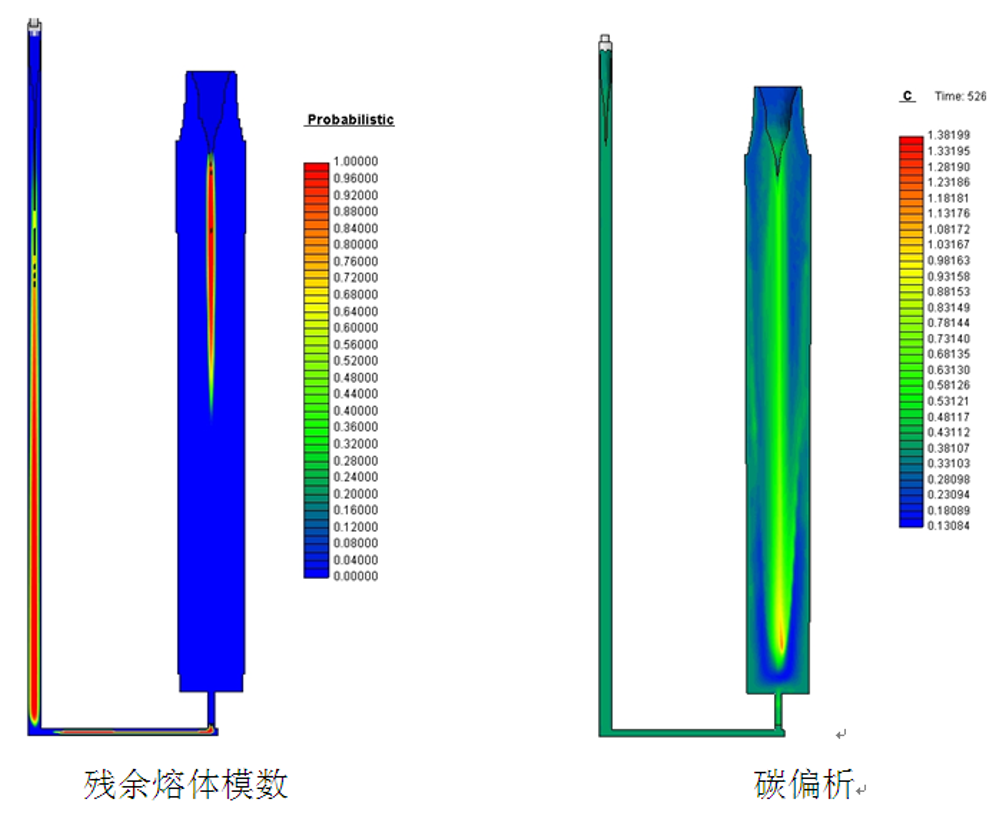
4.3 方案2
Ф500电极坯。浇铸温度1500℃,浇铸速度60cm/s,浇满时间500s,冒口为常规冒口,浇铸后不加发热保护渣,全凝时间6060s,约101分钟。
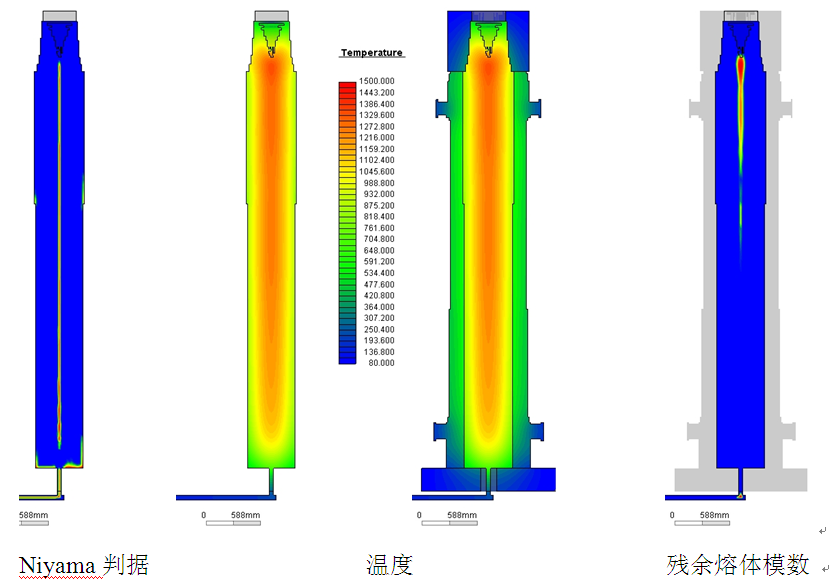
4.4 方案3
Ф500电极坯。浇铸温度1531℃,浇铸速度60cm/s,浇满时间492s,绝热冒口,浇铸后加发热保护渣30分钟,全凝时间13966s,约232分钟
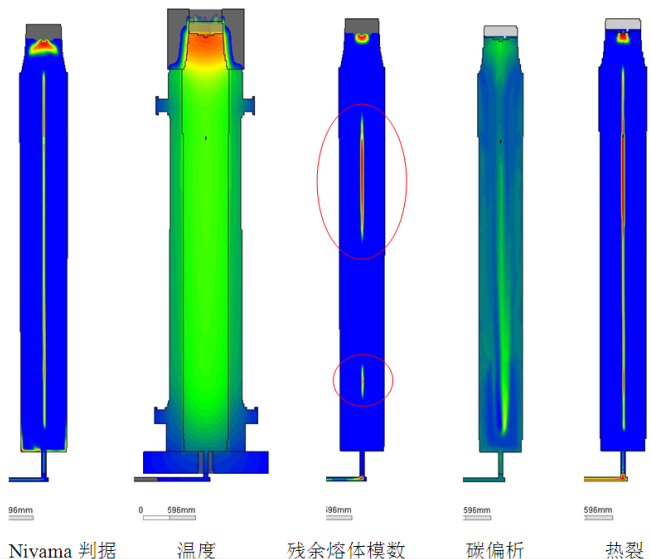
4.5 方案4
Ф500电极坯。浇铸温度1511℃,浇铸速度随充型率变化,浇满时间828s,冒口为绝热冒口,浇铸后加发热保护渣40分钟,全凝时间12521,约208分钟
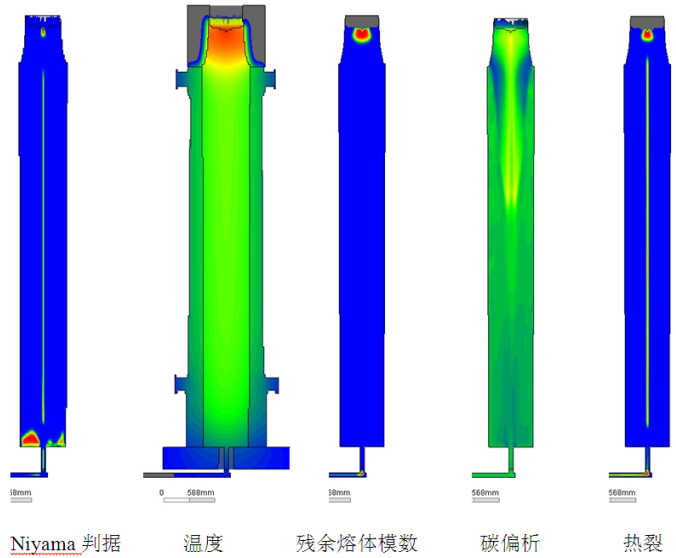
4.6 Ф500电极坯浇铸模拟结果对比
根据上述Ф500电极坯浇铸过程结果对比分析可知,在过热度为40℃、充型时间13.8分钟,采用中频感应加热冒口,可获得质量相对较好的电极坯锭。但由于锭的细长比过于大,且锥度很小,不可避免产生一些中心疏松。如果能够进一步降低浇铸过热度,或增加充型时间,都可以使锭的质量向好的方向转化,但降低过热度将会给铸锭表面质量和浇铸过程带来不利影响。
5.结论
通过对浇注温度、浇注速度和发热时间对铸件质量影响进行了对比研究,结论如下:
1. 随着发热剂的添加,凝固时间有所增长,铸件缩孔疏松缺陷的倾向有所减小;
2. 随着浇注温度的升高,凝固时间有所增长,铸件缩孔疏松缺陷的倾向有所增增加;
3. 随着浇注速度的增大,铸件缩孔疏松缺陷的倾向有所增大;
4. 随着锭模厚度的增加,铸件缩孔缩松缺陷有减少的趋势。
鸣谢作者:辽宁科技大学 胡小东 副教授